Quick Claim Process
Affordable Premium
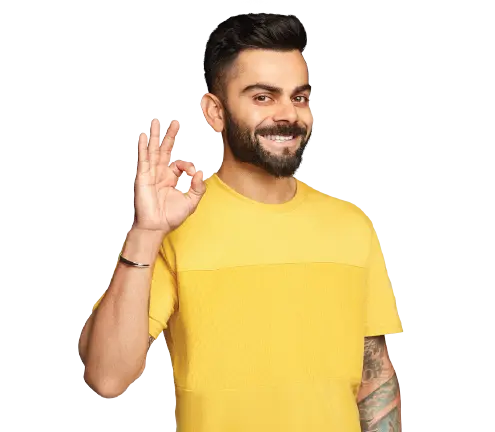
General Insurance
Life Insurance
Claims
Resources
Quick Claim Process
Affordable Premium
A budget significantly influences a business's efficiency, production, and profits. In this regard, standard costing is a valuable accounting method that aids in creating precise budgets for manufacturers. However, since it takes a lot of effort to gather information about actual costs, standard costs are used as the principal justification for standard cost accounting.
To learn more about this costing, keep reading till the end.
Standard Cost Accounting is also known as Standard Costing. It is a type of cost accounting that employs fixed costs for overhead, materials, and labour to calculate the prices of goods and services. The cost of products is often calculated using established rates for materials, labour, and overhead in the manufacturing industry.
Standard costing is a method businesses use to define production target costs and then contrast actual production costs with the targets. Companies might find variations they need to address to improve their production processes by using this comparison to find them.
There are three fundamental aspects of a manufacturing system, which comprise the following:
You can use the following standard costing formula to determine a product's typical cost:
Standard Cost = Material Cost + Manufacturing Overhead + Direct Labour
Here,
Materials Cost = market price per unit x total number of units
Manufacturing Overhead = Fixed Overhead + (Variable Manufacturing Overhead × Total Number of Units)
Direct Labour = employee hourly rate x no. of hours worked x total number of units
XYZ Production manufactures T-Shirts. The authority meets with the team and plans to produce 300 units of T-Shirts in the upcoming year. The team estimates its costs as follows:
Then, the process of standard costing calculation include:
Materials Cost = ₹500 (cost per unit) x 300 (total number of units) = ₹ 1,50,000
Manufacturing overhead = ₹ 50,000 (fixed overhead) + [₹ 400 (variable manufacturing overhead) x 300 (total number of units)] = ₹ 1,70,000
Direct labour = ₹100 (employee hourly rate) x 2 (number of hours to produce one unit) x 300 (total number of units) = ₹ 60,000
Therefore standard cost = ₹ 1,50,000 + ₹ 1,70,000 + ₹ 60,000 = ₹ 3,80,000
Manufacturers use standard costing to develop budgets since it is challenging to estimate the actual costs of making an item before the production process is complete.
Budgets for manufacturing are typically a good approximation rather than the final cost. Also, once manufacturing is complete, the differences are determined by comparing the standard and actual costs. The budget for the following year can then be improved using this information.
When standard costs are used instead of actual expenses, calculating the necessary inventory is made simpler. The cost of manufacturing typically varies from one batch to another during production. A few causes of this include production snags, changes in the cost of raw materials, and adjustments in employees.
Additionally, when using standard costing, manufacturers can determine the inventory value by multiplying the actual inventory by the standard cost of each item. This aids them in estimating the inventory costs that are probably pretty close to the actual expenses.
Even before the production process is finished, standard costing aids manufacturers in setting the prices of the finished goods. Companies may appropriately price their products to generate profits without overpricing them if they accurately view the projected manufacturing costs, including materials, labour, and administrative costs.
Also, manufacturers may easily account for changes in production costs with shifting volumes while maintaining consistent product pricing across batches using standard costing.
Maintaining a company's financial records becomes challenging if it is forced to rely only on actual costs. On the other hand, standard costing makes it easier for businesses to create and manage their financial records.
The business may carry out additional financial actions, such as borrowing and overdrafts, using the information from standard cost calculations because it has an intelligent estimate of projected costs.
Manufacturers utilise standard expenses to establish benchmarks to assess if actual costs fall within these limits. Budgeting is successful if actual costs are within the range of expected costs.
However, if the actual costs differ negatively from the standard costs, the company seeks to improve its production efficiency to reduce these costs in the future.
Besides the advantages, a few disadvantages include the:
Standard costing can be a helpful tool, but it is essential to recognise that it has some restrictions. For example, standard costs could only sometimes represent actual expenses, and businesses might struggle to create reasonable standards. It might also take a lot of time to track. Despite these drawbacks, it can still be helpful for industrial businesses looking to enhance their production methods.
The variation arises because of how frequently the situation changes and how many unexpected factors are involved.
There are three types of standard costing, including:
Here are the main objectives of using a standard costing system:
Use a standard costing-like approach. Estimate future needs like education, debt, and living costs. Then set a standard cost target, and find a life insurance plan that covers it. This ensures financial security without emotional guesswork.
Standard costing helps you estimate and control financial costs. Similarly, term insurance lets you plan fixed premiums over a term. You can match your insurance premiums to your budget more accurately, avoiding overspending or underinsuring.
Definitely. Standard costing is all about expected vs actual cost. You can use it to predict expected medical expenses and compare health insurance plans based on premium vs coverage. This helps you avoid surprise costs or overpaying for features you won’t use.